In solar street lighting systems, the LED light head, as the core component providing illumination, directly impacts lighting performance, lifespan, and overall stability. Customers frequently report issues such as non-functional light heads, making accurate quality testing of LED solar street light heads a critical concern. Below, we outline detailed testing methods.
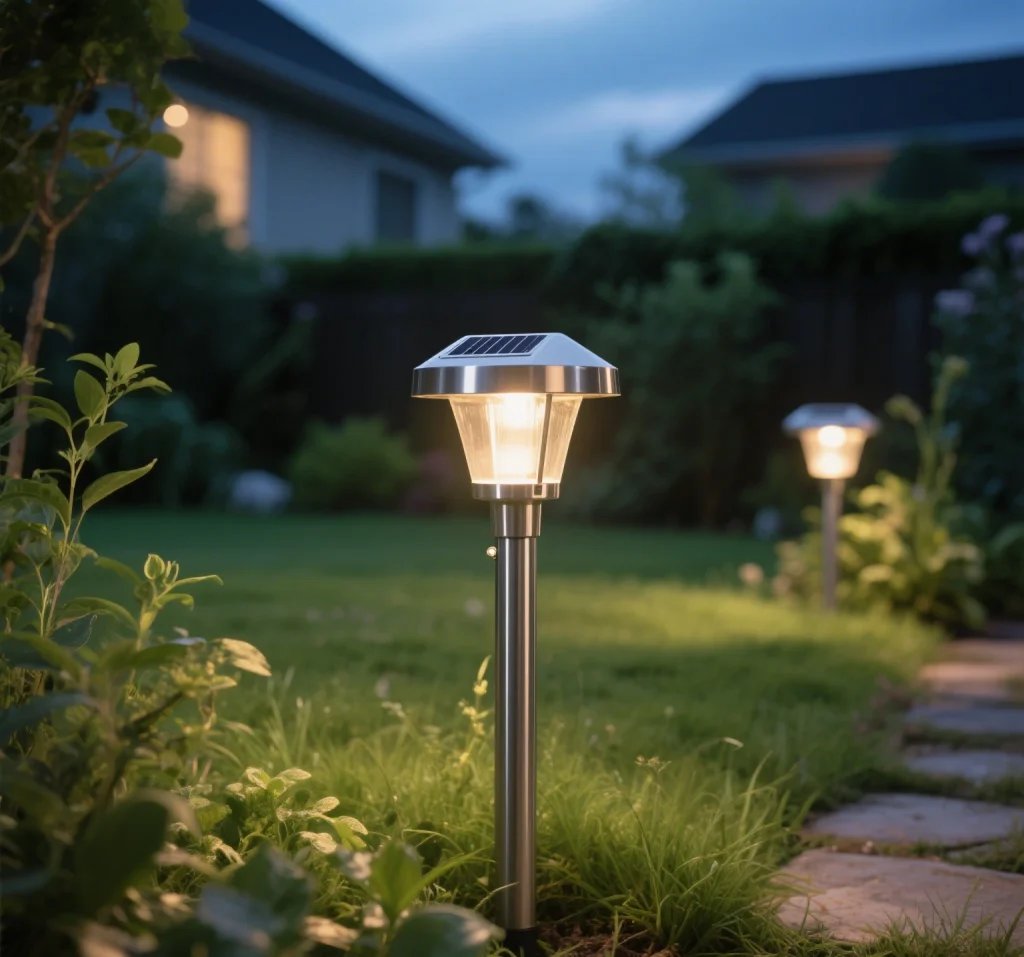
1. Testing Based on Light Head Type
(1) LED Light Heads with Built-in Constant Current Source
- Direct Battery Connection Test: According to guidelines in Design and Application of Solar LED Street Lighting Systems, connect the light head’s positive and negative output terminals directly to the battery output. This test, based on basic circuit principles, checks if the light head can illuminate without the controller. Since controller malfunctions can affect the light head in real-world operation, this step evaluates the light head’s intrinsic functionality. If it lights up, the light head (excluding controller-related components) is generally functional; if not, further investigation is needed.
- Constant Current Source Replacement Test: If the light head fails to illuminate, remove the built-in constant current source and replace it with a new one for another lighting test. As explained in LED Lighting Driver Power Technology and Applications, the constant current source stabilizes current and is a common cause of light head failure. If the light head works after replacement, the original constant current source is likely faulty.
- Controller-Constant Current Integrated Unit Test: If a standalone constant current source is unavailable, use a corresponding controller-constant current integrated unit for testing. This unit combines control and constant current functions. If the light head functions with the integrated unit, the original constant current source is defective. If it still doesn’t light up, the LED chips are likely damaged. This conclusion stems from the system’s operational logic: once the constant current source (or integrated unit) is ruled out, the LED chips become the primary suspect.
(2) LED Light Heads without Constant Current Source
- Controller Replacement Test: Light heads without a constant current source differ in circuit structure and may have configurations like 3-series or more. When suspecting an issue, replace the controller with one from a functioning unit in the same project. Research from Fault Diagnosis and Maintenance Strategies for Solar Street Lighting Systems indicates that controller failures are a significant cause of system issues. If the light head works after replacement, the original controller is likely faulty; if not, further inspect the light head.
- Wiring and LED Chip Inspection: If the controller is not the issue, check the light head’s wiring for damage, short circuits, or open circuits, as these directly affect functionality. Use a multimeter to measure the wiring’s resistance, following Electrical Wiring Testing Standards. Resistance should fall within a normal range; deviations indicate wiring faults. Next, inspect the LED chips. For multi-series configurations, use a battery to test each 3- or 4-series LED group individually. If a chip doesn’t light up but the connected wiring is intact, the chip is likely damaged.
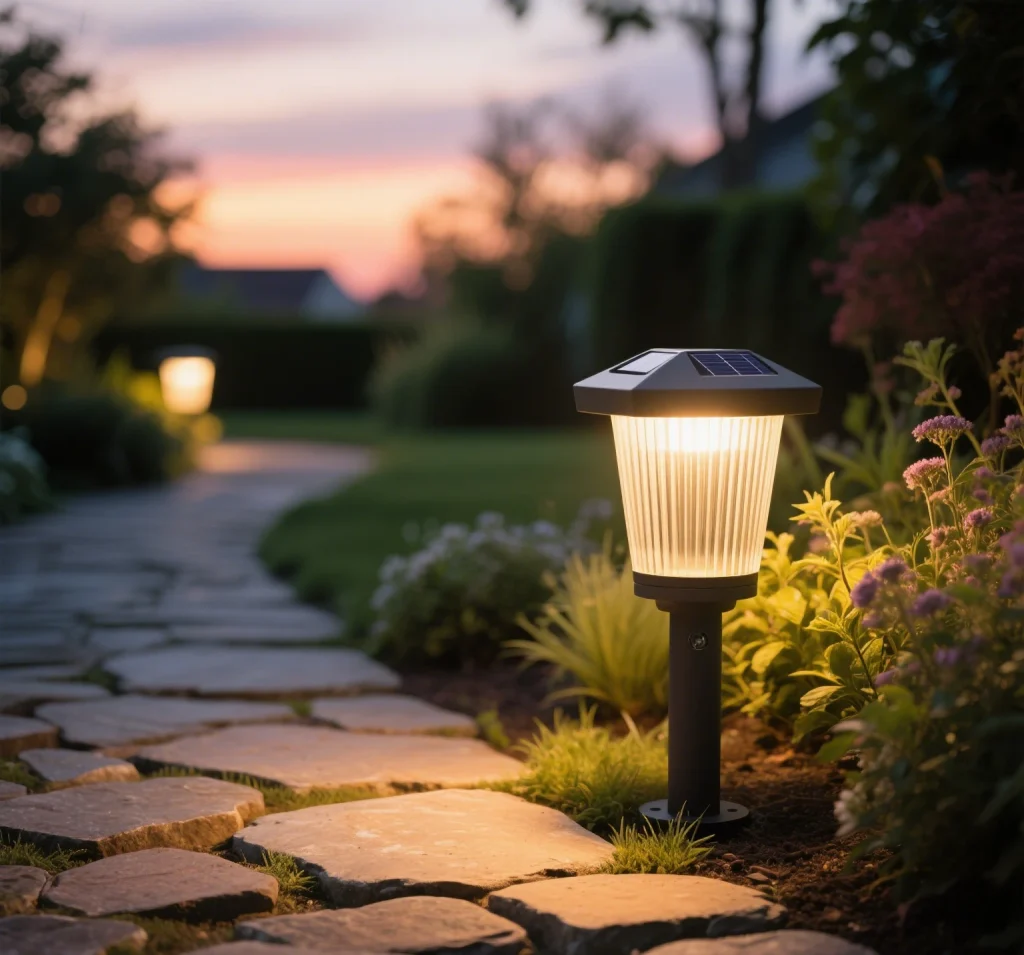
2. Additional Quality Testing Considerations
(1) Appearance and Structural Inspection
- Housing Material and Craftsmanship: According to professional solar lighting websites and industry reviews, high-quality LED solar street light heads typically use durable, heat-dissipating materials like aluminum alloy. This material is strong, resistant to impacts and harsh environments, and effectively reduces LED chip operating temperatures, extending lifespan. Craftsmanship details, such as smooth, scratch-free surfaces and tightly sealed joints without gaps or deformation, reflect quality. Refer to Solar Lighting Appearance Quality Evaluation Standards for initial assessments via visual and tactile inspection.
- Internal Structural Integrity: Open the housing to inspect internal components. Check if the aluminum substrate and plate meet design specifications for size and thickness, as these support and dissipate heat. Per Principles of LED Lighting Internal Structural Design, properly sized components enhance heat conduction and system stability. Wiring should be neat, without loose or tangled connections, and solder joints should be secure, adhering to Electrical Soldering Quality Testing Standards.
(2) Electrical Performance Testing
- Current Stability Test: Use a clamp meter to measure current through the light head during operation. As noted in Current Stability Studies for LED Lighting Devices, stable current is critical for consistent illumination and longevity. The working current should remain within the product’s rated range with minimal fluctuations. Excessive fluctuations can cause unstable lighting or shorten LED chip lifespan.
- Insulation Performance Test: Use an insulation resistance tester to evaluate the light head’s insulation, ensuring safety and preventing leakage-related accidents. Per Electrical Equipment Insulation Performance Testing Standards, insulation resistance should reach the megaohm level. Low resistance indicates potential leakage risks, requiring inspection of insulation materials or wiring for damage.
(3) Optical Performance Testing
- Illuminance Test: Use a lux meter to measure the light head’s illuminance, a key indicator of lighting effectiveness. Different applications have specific requirements; for example, Urban Road Lighting Design Standards specify minimum average illuminance for main roads to ensure traffic safety. Place the meter at a set distance and angle from the light head, compare the measured value to standards, and determine if it meets practical needs.
- Color Temperature Test: Measure the light’s color temperature using a color temperature tester. Color temperature affects visual perception—lower temperatures (yellowish) feel warm, while higher temperatures (bluish) feel cool. Specific settings, like residential or commercial areas, have distinct requirements. Ensure the light head’s color temperature aligns with the intended application.
Customers encountering light head issues at construction sites should consult professional controller manufacturers or solar street light suppliers. Their expertise enables accurate diagnoses and solutions, preventing unnecessary costs from misjudgments and ensuring stable, efficient operation of solar street lighting systems.
Leave a Reply